Home » Company directory » Air Sentry Limited
Air Sentry Limited
Company bio
Air Sentry started as a research partnership in 2000. Andrew Carnegie had innovated within the ITU and OR areas as the Managing Director of Kreuzer (UK), now part of Hill Rom. He noticed a rapid build up of biological material on the upper surface of newly installed service delivery pendant arms. When it became clear these were not due to poor hygiene regimes, he set out to develop a solution to what appeared to be a problem with hospital ventilation design. During the period from 2000 through to 2007 various approaches were tried, including recirculation using HEPA11 filtration, ozone, plasma and UVC. It became apparent that health care clients were looking for assurance and that the only way to supply this is with filtration that offers an assured ‘stop’ to pathogens and also pollutants. The first recirculation systems were deployed in 2007 and immediately met considerable resistance due to HTM03.01. It took long conversations with several members of IHEEM to tune and refine that initial prototype to becoming the basis of a true modular system, which was achieved in 2009.
In 2010 Air Sentry used a cartridge filter with an EN1822 media tested to H14, pre filtration of F9 and a large activated carbon layer. Testing by pathogen research in Leeds gave excellent performance for aspergillus, C.diff and Staph. At 1µm Staph is also a possible surrogate for viruses in the environment. These results are given on this page but it is important to note that Air Sentry achieved 82.1% for Staph in the same facility as SAGE used in November 2020 for the same pathogen. With 20% better performance this makes there 2010 version of Air Sentry significantly better than any other system tested. Today the core module in Air Sentry uses ULPA15 final media, a cartridge with almost twice the surface area and is able to flow a maximum of 1400m3/hr, twice the 2010 figure. Our own testing shows that the performance today is closer to 90%, making our approach significantly better than any other system available globally.
With such high performance, Air Sentry does not need to use UVC to compensate for lower grade filtration. We found during our initial development that UVC is excellent within duct work but it requires an exposure time to work at faster flows. To be truly valid within a filter system UVC therefore requires a long powerful array and Air Sentry avoids this additional cost and complication by simply using a single change filter cartridge. With a filter life of 24 months this reduces service personal exposure to risk, whilst maximising end client utilisation with improved reliability.
Each Air Sentry base module is geared so that is can be wall, floor or ceiling supported, making the system ideal for use in areas where a short term solution is required or where low void areas limit the design options.
To each module the client can specify a negative or positive pressure differential pressure module. Each module comes equipped with its own fan and filter thus increasing potential air delivery rates.
Each base module can also accept an HVAC connection, making it possible to design Air Sentry into an existing HVAC system without back pressuring the main AHU, whilst still offering an ultra clean end environment.
Because Air Sentry is genuinely UK manufactured we have the capability of adapting the system to an end clients bespoke requirements. This has included BMS integration (BMS) and adding in a 20% ‘filtered ‘fresh air’ module where pressure differential isn’t required.
Each Air Sentry system is truly modular and has a design life in excess of 25 years. Made from steel, the system is extremely robust. We have even had a mobile unit accidentally crushed by a CT arm with several tonnes of force. This broke a wheel (as intended in our design) and the unit continued to function without anything other than cosmetic damage.
In September 2021 we are launching ‘K9’ which has a patent application pending for its design. Most competing systems fail to understand that room dilution, and therefore mixing, is essential for enhanced performance. Air Sentry does not simply rotate air next to the system unit but achieves a whole room rotational flow. This flow reaches to lower corners and cleans an entire area. In use areas using Air Sentry normally reach an equivalent cleanliness to ISO EN Level 7, without the associated 60 ACH.
Each Air Sentry unit is quiet in normal use and uses a minimal amount of power (around 70w) in normal running. The system is also able to be used at maximum when required. Clients during the pandemic have been using this to reduce fallow times between patients.
By using Air Sentry to maintain an adequate level of air bio security during an aerosol generating procedure, the risk of nosocomial transmission is reduced. Once the patients leave, turning Air Sentry to maximum can produce rapid room cleaning, reducing fallow times in many areas to well under ten minutes, often nearer to five.
We have systems in use across the NHS in most clinical areas. We also area able to offer post installation certification of performance, included as part of our service.
Key services
Resources
Available work experience opportunities
Current vacancies
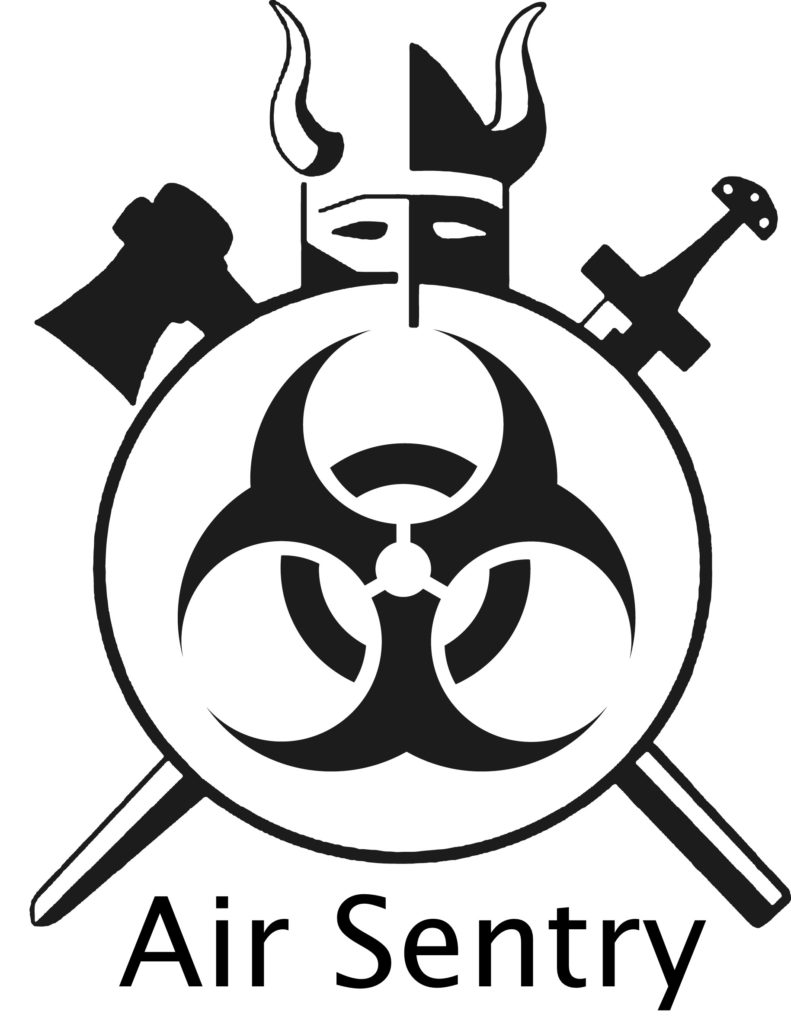
Company Address
Unit 1, Manor Stables
West Street
Great Somerford
Wiltshire
SN15 5EH
Telephone
Website
Sales contact
Name: Andrew Carnegie
Telephone: 01249 721422